How 3D Laser Scanning Cuts Construction Costs
The San Antonio company Reckon Point uses robots to scan building interiors. It joins a crowded field of competitors making inroads with laser technology
“Human measurements”, for lack of a better term, have long added cost to real estate development. Developers must pay architects to measure the inside of buildings and surveyors to measure the surrounding land, adding time and human error to the process. For decades, different tech companies have tried to replace this with 3D laser systems that scan buildings and land to create exact computer renderings. Now the technology is reaching mainstream acceptance.
Recently during a 2-week trip through Texas, I interviewed one firm that provides it in this increasingly competitive landscape.
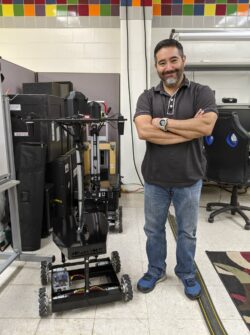
ReckonPoint, based in San Antonio, is owned by Gabe Garza, an entrepreneur who previously worked with the military on remote sensing. He has now used that tech to build a robot that specializes in indoor mapping.
The process starts when a client who is renovating or constructing a building needs measurements. ReckonPoint sends a 4-wheeled machine that can roll through the building taking laser scans. The machine then uploads the data to a computer, creating a 3D visualization similar to what is done with AutoCAD. The development firm can use the machine to continue taking measurements throughout the course of the project and return them to ReckonPoint once done. Garza said the entire cost of renting the machine is $40,000, and that since the company’s 2014 founding, he has found many clients who use it for large projects in the U.S. and Mexico.
The primary advantage ReckonPoint has over normal surveying, Garza told me from his bunker-like startup space in Port San Antonio, is down-to-the-millimeter accuracy. Conventional building survey work is done manually with tape measures. ReckonPoint’s robots utilize a method known as LIDAR “point cloud” scanning. LIDAR is a remote sensing technology that takes hundreds of thousands of images per second. This creates a cloud of images that are assembled to provide a high level of detail, capturing various elements of buildings such as windowsills and sinks. The end product is a 3D model, known as Building Information Modeling.
“Architects tell us that they have to go back 5 or 6 times to take more measurements,” says Garza, adding to the expense of construction. “We don’t have to worry about going back a second time … all they have to do is go back to the point cloud and all the data is there.”
This sort of scanning is particularly advantageous for old building retrofits, otherwise known as “adaptive reuse.”
“Typically what happens is we’ll get an architect who’s interested in upgrading an old building,” Garza says. “90% of the time old buildings have no blueprints or CAD models.”
Simon Barnes, a British architect, noted in 2009 that this is a common problem for historic preservation projects.
“When they do exist, they are most often hard copy blueprints that may have limited value for preservation, rehabilitation, restoration, or reconstruction efforts tied to today’s efforts.”
But Garza said 3D laser scanning can be used to check construction progress on newly-erected buildings, too. As each floor is completed, the robot scans to ensure its measurements are conforming to the initial plan. Garza says it is particularly beneficial for modular prefab construction, where measurements must be precise.
While ReckonPoint focuses on indoor surveying, he hopes in the future to apply 3D laser scanning to the outdoors through drones. He thinks this technology, which is already used somewhat in land surveying, will disrupt an industry that still relies on manual electronic distance measuring.
“If equipment like ours got to survey-grade level,” says Garza, “I don’t know if it would totally put [surveyors] out of business, but I think either they would be using this, or the civil engineering company might be doing this themselves.”
ReckonPoint is far from the first company to provide 3D laser scanning services for real estate. In a piece for the blog Digital Builder, Grace Ellis writes that laser scanning technology dates back to the 1960s, although it was not used for design and engineering until the 1990s.
“It’s just now starting to gain serious traction in the construction industry,” she writes. “The demand for laser scanning in construction was only 20% in 2016. In 2017, demand minimally increased to 22%; however, a year later, in 2018, it spiked to 57%. The annual growth rate for 3D laser scanning is believed to be around 15% currently. Valued at $3 billion in 2016, it’s a market that is expected to grow to $10 billion by 2024.”
Other companies besides ReckonPoint that work in the space include Carto, Sanborn, and ATFF. Perhaps more interesting is that Google and Apple, says Garza, are both experimenting with indoor mapping technology. Given their immense use of GIS thus far to map the outdoor world, that venture could be interesting.
Either way, indoor mapping via 3D laser scanning is already transforming home construction, producing up to 50% in cost savings. Market innovation has streamlined this particular aspect of construction even as government regulations make everything else about construction harder.
Catalyst articles by Scott Beyer | Full Biography and Publications